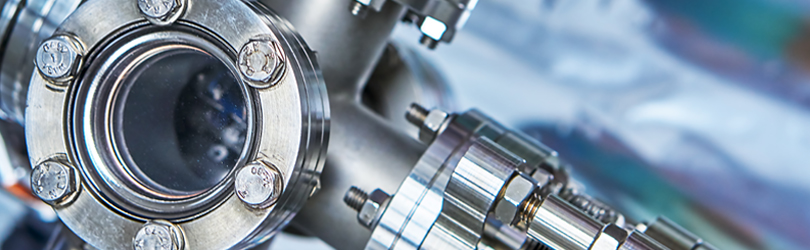
The ongoing debate for years has been “What is the best method to measure high vacuum? Hot cathode (Bayard-Alpert) or cold cathode?” While hot filament gauges are popular and used in various applications, the cold cathode has unique operating characteristics that often make it a better choice. Cold cathode gauges are economical because they rarely need to be replaced, are not subject to damage due to accidental in-rushes of air, have no X-ray-induced errors at ultra-high vacuum (UHV), and do not have a filament that outgases or reacts with process gas. Their control/sensing electronics are also simpler and thus more reliable than Bayard-Alpert electronics. This article aims to provide a brief history of cold cathode measurement technology and provide an application template for gauge selection. Some of the myths will be clarified such as starting/ignition, measurement inaccuracy, and magnetic interference associated with cold cathode technology.
Just as there are different and evolutionary vacuum sensors in hot cathode technology (Triode, Schulz-Phelps, and Bayard-Alpert), each with their own unique operating characteristics, there are distinct differences in the classification of cold cathode gauges. Categorizing all cold cathodes into the same operation mode is erroneous. This misconception of cold cathode measurement technology has been kept alive more by competitive corporate fervor rather than scientific fact. While most cold cathodes used today are magnetrons, there are several different types of magnetrons, each with their own measurement and operating characteristics. A magnetron is a device with an axial electron emitter (cathode) and a coaxial cylindrical anode with an axial magnetic field superimposed.
The earliest form of cold cathode ionization gauges was first constructed as a simple discharge device, which was a glass-enveloped tube with discharge plates (electrodes) at either end. It had a measurement range of 20 to 10-3 Torr. The glass envelope was connected to a vacuum system. The electrodes were connected to a fixed high-voltage power supply. Electrons from the negative electrode collided with gas molecules to produce ions, resulting in a discharge between the two electrodes. The amount of current in the discharge was proportional to a vacuum reading. All subsequent cold cathode/magnetrons versions use this characteristic to measure vacuum. The evolution of this measurement technology consists of a series of magnetic field improvements and electrode placements. Each step of the evolution improved on the previous design by eliminating or minimizing their negative characteristics.
Penning Ionization Cold Cathode
The first refinement of the discharge tube resulted in the Penning ionization gauge (PIG). This utilized a magnetic field to lengthen the travel of electrons, thus increasing the probability of ionizing collisions and more stable discharge fields. The original version of the Penning gauge was developed from 1936 to 1937. As schematically shown in Figure 1, this gauge is characterized by the orientation of the magnetic field lines (B fields) in relation to the anode. Later work by Penning and Nienhnis led to an improved PIG with a cylindrical anode, giving a more stable discharge.
Penning gauges like the Televac®️ 7B Penning Cold Cathode measure vacuum in the range of 10-3 to 10-7 Torr and are popular today because of their robustness, with a higher tolerance to contamination, and the ability to be dismantled and cleaned, extending the gauge’s lifespan. The Penning cold cathode gauge provided a robust alternative to the hot filament or Bayard-Alpert gauge. Its discharge, however, would extinguish when used at vacuum levels below 10-7 Torr. This is a problem that would be solved years later but fostered the proliferation of Bayard-Alpert sensors, which had none of these measurement limitations. Also aggravating the development and acceptance of cold cathodes were the difficulties of designing reliable 3 to 5 kilovolt power supplies and converting the discharge current into a user-friendly vacuum readout, which was only an “analog” meter at the time.
The Bayard-Alpert gauge’s collector current was a linear function of vacuum, while the cold cathode sensor was non-linear. The Bayard-Alpert readouts had linear meter scales and offered better resolution than the non-linear cold cathode meter scales. As log amplifiers, microprocessors, and digital displays became common over time, the display of meaningful and accurate vacuum measurements became a moot point, but it took decades after the initial development of the PIG for this to happen.
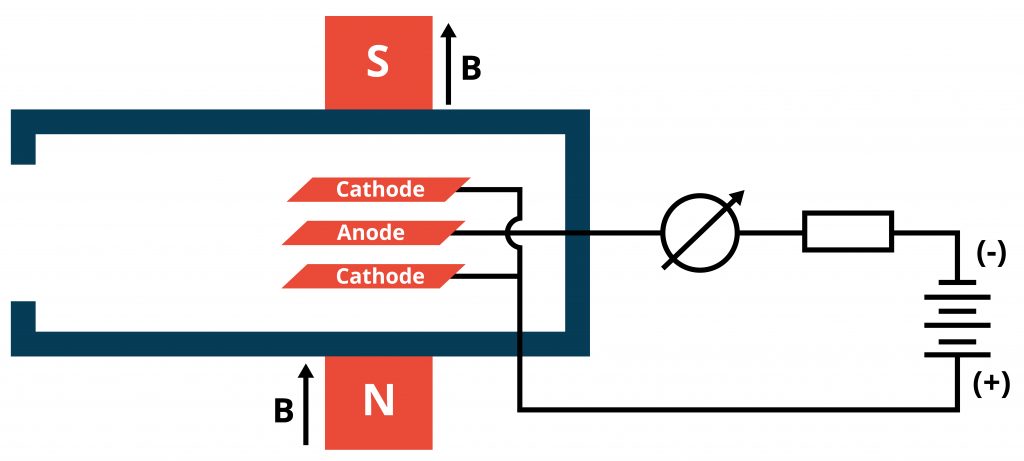
Figure 1 – Penning Cold Cathode Vacuum Gauge
Inverted Magnetron Cold Cathode
The next major improvement in cold cathode technology was the inverted magnetron gauge (IMG). This sensor was developed from 1950 to 1958. The design incorporated a magnetic field that is parallel to the anode and provides operational improvements over the Penning gauge. Figure 2 illustrates a basic inverted magnetron ionization cell. A cathode surrounds the anode, centrally located. The magnetic field in this configuration is parallel to the anode. The resultant crossed magnetic and electric fields provided an enhanced stable operating range and improved starting characteristics at high vacuum. Further advancements in inverted magnetron technology, developed in 1958 by Redhead, created an extraordinary measurement device capable of measuring vacuum to 3*10-13 Torr. This design overcame the problem of starting at these very low pressures by confining the electrons to the discharge region. NASA subsequently used a version of this gauge in space exploration. The commercially available IMGs of this period measured to 10-8 Torr with vastly improved characteristics over the Penning gauge. At the same time, the Redhead inverted magnetron provided a glimpse of what was possible with cold cathode technology.
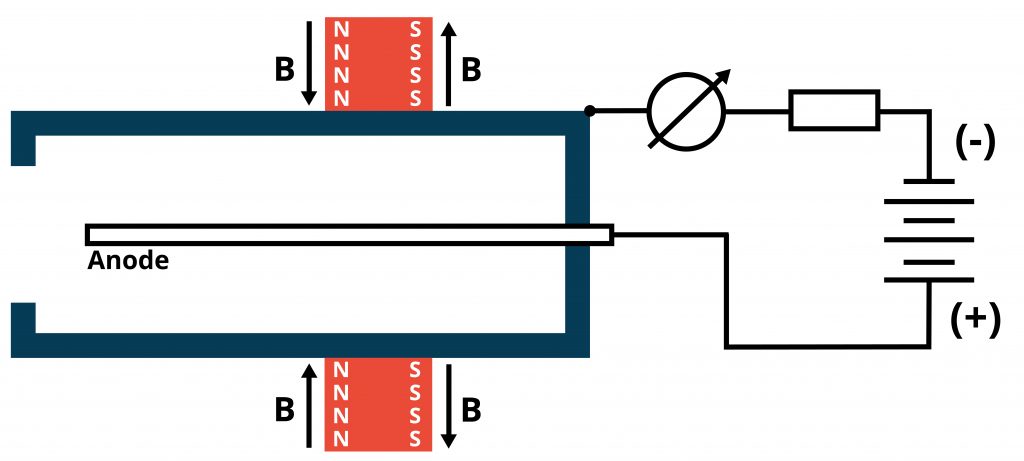
Figure 2 – Inverted Magnetron Cold Cathode Vacuum Gauge
Double Inverted Magnetron Cold Cathode
While the inverted magnetrons improved performance over the Penning gauge, dependable and sustained measurement operation below 10-8 Torr was still an issue for most cold cathode vacuum gauge manufacturers. Careful selection of magnets and manufacturing tolerances made small improvements, but a sustained and reliable discharge at 10-9 to 10-11 Torr was not easily or economically attainable with many inverted magnetron vacuum gauge designs.
A double-inverted magnetron was developed and patented in 1996. This provided consistent and reliable operation below 10-8 Torr as well as little to no external magnetic field while increasing the size and strength of the magnetic field inside the sensor. This provided improved sensitivity. Starting times were also improved over prior designs. Figure 3 represents the construction of a double inverted magnetron. Opposing magnets maintain two separate magnetic fields, creating two separate inverted magnetron cells. The probability of ionization increases as an ionized particle moving out of one cell has a 50% chance of ending up in the other cell. Electron currents are essentially double those produced by a single inverted magnetron cell, providing a better signal-to-noise ratio, and enabling the electronics measurement range to extend to 10-9 Torr and beyond. Measurement capability below 10-9 Torr combined with significant improvements in high-voltage power supplies, low current measurement, and magnetic materials eliminated past issues, making the double-inverted magnetron the most modem approach to practical high vacuum measurement.
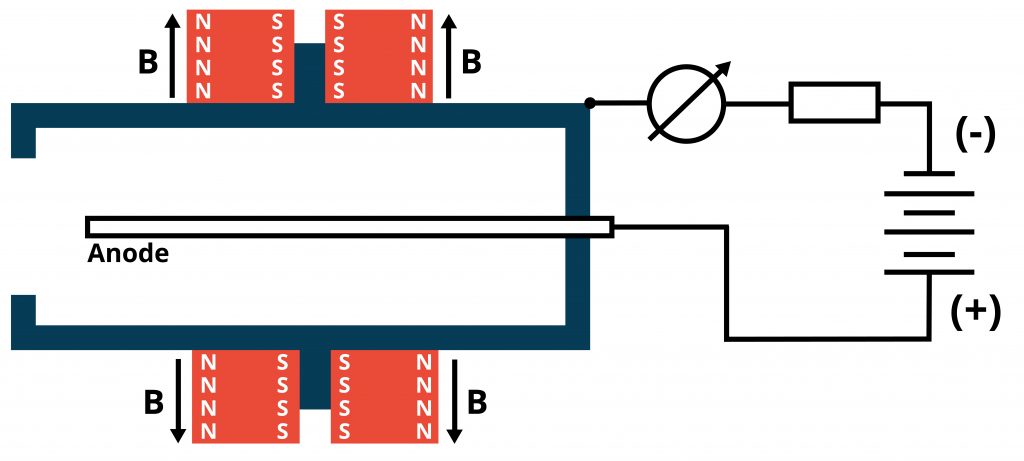
Figure 3 – Double Inverted Magnetron Cold Cathode Vacuum Gauge
Modern double inverted magnetrons are vastly different gauges from the early Penning gauges and inverted magnetrons. They measure a vacuum range greater than a conventional Bayard-Alpert gauge while providing comparable accuracy and very good long-term stability. Cold cathodes are not subject to ESD (electron-stimulated desorption) errors. ESD is a condition that randomly appears in Bayard-Alpert gauges and causes errors of at least 10% at 10-7 Torr, with errors worsening in deeper vacuum approaching 10-10 Torr. It is a problem that makes work at low pressure substantially more difficult.
Double inverted magnetrons are better suited for high and UHV vacuum measurements because they are not subject to X-ray errors and filament outgassing. At a pressure of 2*10-10 Torr, a Bayard-Alpert gauge with an X-ray limit of 2*10-10 Torr will have an approximate measurement error of 100%. This error becomes more pronounced as the true pressure drops.
Unlike Bayard-Alpert gauges, The Televac®️ 7E, 7F, 7FC, and 7FCS Double Inverted Magnetron Cold Cathode Vacuum Gauges are resistant to inrushes of gas, cleanable, and have a minimal stray magnetic field. The 7FCS is specially designed to turn on at ultra-high vacuum (UHV) for applications that require ignition in the 10-8 Torr range or higher vacuum, where the 7FCS will turn on in less than five seconds.
Cold cathode measurement technology has evolved significantly from the first Penning ionization gauges. These modern gauges provide accurate, repeatable, and reliable measurement results. Double inverted magnetrons reliably measure a wider vacuum range than most Bayard-Alpert gauges and are not fraught with X-ray or ESD errors. Most versions can be cleaned, repaired, or rebuilt to provide years of service under conditions that are adverse to the operation and longevity of a Bayard-Alpert gauge. One of the most important but often overlooked aspects of modern cold cathodes is that they reduce cost by removing the high cost of frequent Bayard-Alpert gauge replacement.
Application Suitability
Operational Conditions | Bayard-Alpert or Cold Cathode | Reason |
Resistance to Accidental Damage | Cold Cathode | Cold cathodes have a robust metal design (compared to glass or unshielded/nude Bayard-Alpert gauges) and are resistant to damage from inrushes of gas. |
Corrosive Gases | Cold Cathode | Cold cathodes have no high temperature filament to react with corrosive gases. |
High Contamination Processes | Cold Cathode | Cold cathodes are cleanable for an extended lifetime, and there is less effect on their accuracy than Bayard-Alpert gauges when exposed to the same amount of contamination. |
Vibration | Cold Cathode | Cold cathodes have no delicate structures that can vibrate, move, or break like the fine wire filament and grid assemblies in a Bayard-Alpert gauge. |
UHV Measurements | Cold Cathode | Cold cathodes have no filament so outgassing is significantly reduced, and they have better long-term stability than Bayard-Alpert gauges because there are no fine wire structures that geometrically change over time, compared to the fine wire structures of a Bayard-Alpert gauge that will move and geometrically change over time, impacting performance. |
MTTF | Cold Cathode | Cold cathodes gauges have a higher MTTF because they do not have a filament that can burn out like a Bayard-Alpert gauge, the control electronics are also less complex leading to a lower electronics failure rate. |
Highest Accuracy | Bayard-Alpert | Commercially available hot filament gauges typically have an initial accuracy of around ±10%, whereas commercially available cold cathode gauges typically have an accuracy of around ±30% over the entire lifespan of the vacuum gauge. |